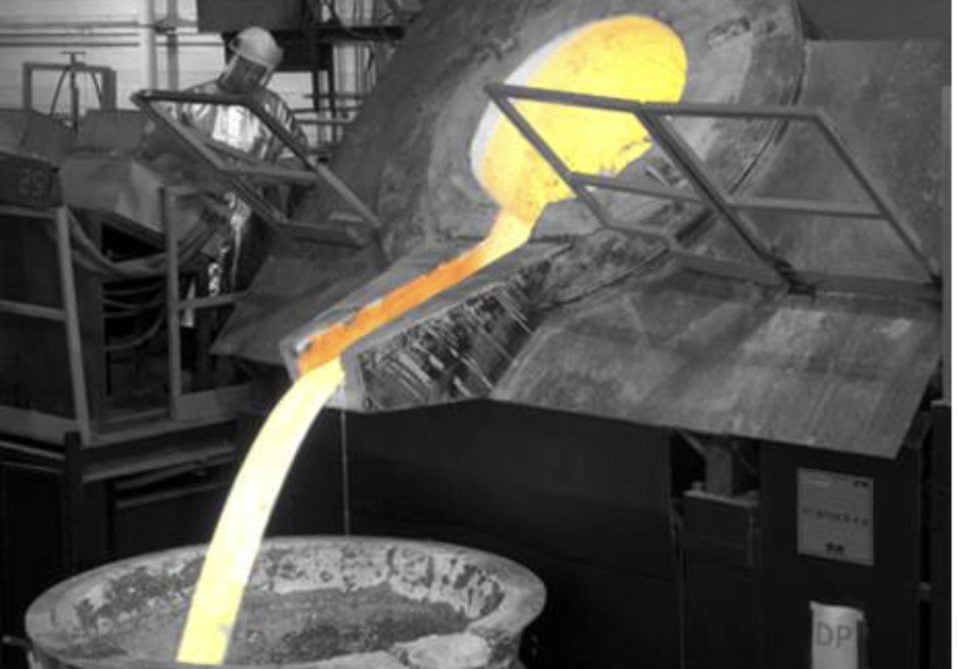
In April, US polysilicon producer Highland Materials secured US$256 million in tax credits to build a new polysilicon factory in north-east Tennessee-the first greenfield polysilicon plant to be announced outside of China for many years.
The funding was part of the US Department of Energy (DOE)’s award of 48C tax credits, announced earlier this year under the Inflation Reduction Act (IRA), to support more than 100 projects in the acceleration of clean energy manufacturing and recycling at industrial facilities. This included US firm Highland Materials’ facility, which aims to initially produce 16,000 metric tons per year of solar-grade polysilicon, as part of efforts to help foster a vertical solar PV supply chain in the US.
Unlock unlimited access for 12 whole months of distinctive global analysis
Photovoltaics International is now included.
- Regular insight and analysis of the industry’s biggest developments
- In-depth interviews with the industry’s leading figures
- Unlimited digital access to the PV Tech Power journal catalogue
- Unlimited digital access to the Photovoltaics International journal catalogue
- Access to more than 1,000 technical papers
- Discounts on Solar Media’s portfolio of events, in-person and virtual
Or continue reading this article for free
Highland Materials plans to start construction at the project early next year and reach commercial operation in late 2026. This timing fits with new solar wafer production in the US, which will likely take two years to get underway.
Richard Rast, president of Highland Materials, tells PV Tech Premium that the company will use a unique segregation technique instead of the most common method of polysilicon production, the Siemens process.
Rast says this process uses metallurgical-grade silicon as its feedstock to create polysilicon, which other firms can then use to make solar wafers.
Historical connections
Highland Materials’ technique evolved out of the aluminium alloy industry and was demonstrated in a factory in Canada back in 2011-12 by a company whose technology is now incorporated into Highland Materials.
“That’s what’s different about the approach that we use,” says Rast. “So, in really simple terms, we’re melting silicon and aluminium together and using a naturally occurring process of segregation, where the impurities in the silicon migrate into the aluminium.”
The Highland Materials management team includes several former leaders of Silicor Materials, which was formed by California-based Calisolar’s acquisition of Canadian company 6N Silicon. The leadership team can draw on a range of experience across the North American silicon sector.
For example, Silicor operated a large-scale pilot polysilicon production project in Canada between 2010-2014, and brought a factory in Iceland close to construction, with funding and engineering work complete. However, when silicon market pricing collapsed in 2016-2017, the project was discontinued and has been dormant ever since.
Highland Materials is a new company that acquired the technology from Icelandic investors, who had invested in Silicor, and is building on top of the silicon purification process engineering work and material science work developed by these former companies back in the 2000s.
“It is a little different than the way people do today, but it enjoys a lot of benefits,” says Rast. “One of the reasons that we were able to secure the funding is because of the opportunity for innovation.”
Keeping up with n-type efficiency trends
However, this has been a challenging sector for other companies in the past. Those working on upgraded metallurgical silicon technology in the past “never really got into massive commercial production” and “it was a bit of failure”, says Jenny Chase, solar analyst at BloombergNEF.
Chase remains sceptical about the potential for future innovation in the sector, because the market has moved on. Instead of industry focusing on multicrystalline wafers for solar modules, today’s market is dominated by monocrystalline, which requires a higher degree of purity.
Likewise, when Silicor worked on polysilicon production in 2010-11, the PV industry’s focus was on p-type solar cells, which required lower purity polysilicon than the high-efficiency n-type solar cells that have become the norm today.
Yet if Highland Materials can make this technology work, it would be a step forward, as it should be produced with a lower energy per kilogram than the Siemens process, or the alternative fluidised bed reactor technology, which is technologically difficult, and intensive for both energy capex.
‘It’s like blended whisky’
When asked about the push for high-purity polysilicon for high-efficiency solar cells, Rast says the company had material leftover from its Canadian factory stored at Fraunhofer ISE in Germany and has proven through tests that even the polysilicon produced in 2010-11 by the Canadian factory would have met the n-type specifications of the present day.
The company has been working for a year to produce new cells that meet the n-type specification, and has done tests with labs in the US, France and Germany to verify performance. In addition, the US’ National Renewable Energy Laboratory (NREL) has been tracking actual performance of cells produced as far back as 2012 to verify that the silicon is holding up as a functional equivalent of silicon produced from the Siemens process.
Highland Materials is now working with wafer manufacturers and cell producers, and sharing the results of the test work done in Europe with third parties, such as Fraunhofer ISE and French Lab CEA, over the last six months. It is working on a variety of different opportunities for off-takers, but Rast could not provide further information on this.
Rast does note, however, that company’s product would not require the blending of polysilicon from multiple sources, despite blending being a very common process in the production of wafers, as it allows producers to minimise waste by using scraps leftover from the ingot process, and acquire materials from multiple suppliers in the supply chain.
“It’s like blended whisky,” says Rast. “You get the same mix at the end of the process every time regardless of what happened in one individual barrel. There are practical aspects to it and there are consistency aspects to it.”
A US supply chain
The Tennessee project was made feasible by US trade restrictions and the incentives offered through the IRA, which created an economic opportunity to build new production capacity in the US that’s focused predominantly on the US market.
“There’s a huge opportunity for new polysilicon capacity within the US or within North America,” adds PV Tech head of research Finlay Colville. “Potentially, it’s more important for the US to have polysilicon manufacturing than it is a lot of the new module capacity that’s going in at the moment, with a large part of funding from Chinese companies making modules in the US.”
Given how close polysilicon is to the start of the value chain, to have new entrants gain investment, who are focused specifically on serving the solar industry, rather than the semiconductor industry, could be “a game changer” for US aims to have a value chain of US-made product for its own market, says Colville.
For years there has been very little new investment in the western world or outside China for new polysilicon capacity. German polysilicon producer Wacker and Korean firm OCI, which has a plant in Malaysia, have built no new capacity for solar in over a decade.
US firm Hemlock Semiconductor’s focus has always been the semiconductor industry, rather than solar. Meanwhile, US-based REC silicon has had its plant in Moses Lake mothballed for a few years until recently.
Chase notes there have been a couple of polysilicon announcements in India, but remains “dubious” about these ventures given the difficulties of making polysilicon.
“So, for a new company to raise funding to manufacture polysilicon specifically in the US for the solar industry is a big deal,” adds Colville.
International tensions
However, while Rast hopes that Highland Materials will be able to explore markets outside the US, polysilicon manufacturing has been difficult for companies around the world since China retaliated against US anti-dumping countervailing duties on Chinese and Taiwanese PV modules back in 2013, with an import duty on polysilicon coming into China.
This hit the businesses of Hemlock and REC silicon to the point where REC Silicon had to shut down its operations in Moses Lake. Eventually, says Colville, due to almost 100% Chinese domination of wafer production, companies wanting to sell polysilicon to the solar industry would have to ship into China, so doing so became almost economically unviable.
This situation would have persisted were it not for the introduction of the IRA, and the expansion of wafer and cell manufacturing in the US, to create a market to which polysilicon could be sold.
“The IRA now is driving the sales channel for US-made polysilicon without having to ship outside the US,” adds Colville.
The Tennessee facility announcement comes at a time where polysilicon prices continue to decline and are expected to decline further while the prices of wafers, cells and modules have also fallen rapidly in succession, as reported by PV Tech Premium’s PV Price Watch this month. Moreover, the prices have even fallen below production costs of some companies.
“It’s still going to be challenging to make good margins when manufacturing,” warns Colville. “Polysilicon pricing has been trending downwards. At present, pricing in China is well below US$10 per kilogram.
“The likes of Wacker, Hemlock, have got premium right now because that polysilicon is used for modules that end up back in the US selling at a higher price. So, there is a kind of 2x premium at present on western-made polysilicon, but there’s no guarantee that that premium is going to be around in three years’ time. With any investment there’s risk and this is no different.”
“This is probably essential to enable a US supplied energy transition, if they really want to get serious about it,” adds Chase. “It’s taking a risk and potentially, the payoff would be getting a new manufacturer with new tech in America. The key to China’s success is it actually builds the factories instead of talking about [it]. It turns out, it’s very hard to make anything if you don’t build any factories.”