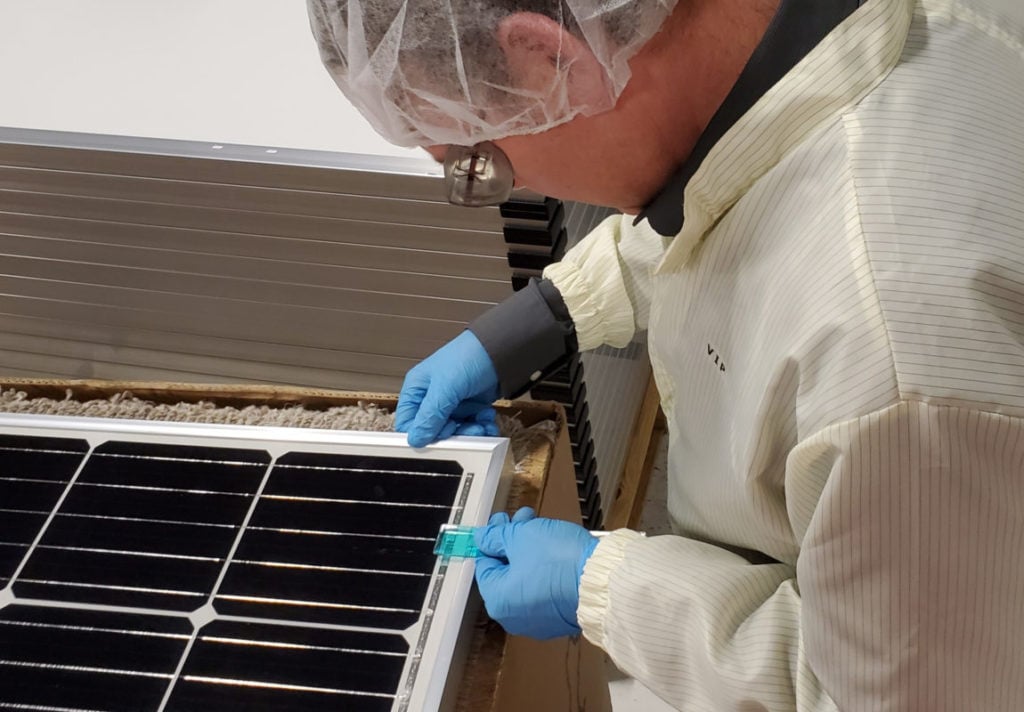
As PV module technology has evolved, so too have the quality challenges associated with the new technologies that have appeared, matured and been superseded. Fei Lu and Stephen Xuereb of PI Berlin draw on over a decade of experience with an overview of the present trends in module quality assurance and likely future challenges as technology continues to change.
Within the last decade, PV module technology has changed and developed drastically. After years of similar-sized 60- or 72 poly-crystalline AL-BSF p-type cell modules, there has been a dramatic shift in size and cell technologies. While quality has continued to improve, the fast-paced changes have introduced new issues (and some old ones from the past) that the industry is currently addressing. PV module manufacturing has experienced a remarkable expansion over the last decade, increasing tenfold globally to meet the increasing demand for renewable energy.
Unlock unlimited access for 12 whole months of distinctive global analysis
Photovoltaics International is now included.
- Regular insight and analysis of the industry’s biggest developments
- In-depth interviews with the industry’s leading figures
- Unlimited digital access to the PV Tech Power journal catalogue
- Unlimited digital access to the Photovoltaics International journal catalogue
- Access to more than 1,000 technical papers
- Discounts on Solar Media’s portfolio of events, in-person and virtual
Or continue reading this article for free
According to International Energy Agency (IEA) forecasts, this trend is set to continue at an elevated pace, with investments in the pipeline set to increase global solar module manufacturing capacity from 640GW in 2022 to over 1,200GW in the medium term. This growth has led to new module manufacturers and their sub-suppliers in the supply chain, including new factories being set up rapidly across Asia.
PI Berlin has been in a unique position during the past ten years monitoring the effects of this rapid growth in terms of product quality. Independent quality assurance of manufacturing processes and materials is crucial to assure the reliability and long-term performance of PV modules.
The experience and knowledge presented in this article will share insights and trends in quality that PI Berlin has observed through factory-based quality assurance on over 100GW of PV modules and the quality of over 15GW of global PV systems. The quality data below will show the defect trends and reflect technology and product innovations within the industry.
The importance of quality
The PV industry has faced several major challenges in the past few years including:
- Changes related to new materials, such as new solar cell structure (n-type solar cells), new encapsulant materials (Polyolefin, and PEP which is a mixture of polyolefin and ethylene-vinyl acetate)
- Changes related to manufacturing processes for new technologies such as tunnel oxide passivated (TOPCon) and heterojunction (HJT)
- Lack of long-term durability results for new technologies like TOPcon and HJT
- Lack of physical understanding of failure mechanisms that occur with new solar cell structures
- The adoption of bifacial glass-glass modules instead of monofacial glass/ backsheet
- The introduction of ultra-large modules based on super-sized silicon wafers, which has proliferated in number and size of module types in the market and triggered new rounds of quality testing and changes in system integration
- Supply chain disruptions due to the COVID-pandemic and geopolitical 19 conflicts resulting in more suppliers and factories to meet demand
- Requirements for higher standards of environmental and social governance, including greater transparency in the silicon supply chain
Supply chain disruptions in the industry have increased buyer and investor concerns, not only for quality, but also for completing projects on time. Significant project delays have been observed due to COVID-19 restrictions, increasing shipping costs, shortage of shipping capacity, new import rules, government tariff circumvention investigations or supply chain traceability requirements.
Apart from delays, these disruptions have resulted in direct challenges to module quality coming from unexpected or last-minute switches in manufacturers, factory locations, module types or bills of materials. Manufacturers have also increasingly had the upper hand in supply negotiations which inevitably means that some quality requirements, demanded by the buyer, may have to be sacrificed to secure supply.
It is crucial to pay close attention to quality to ensure the longevity and reliability of a PV project. Completing PV projects using alternate bills of materials or working with unfamiliar suppliers heightens the concerns of buyers and investors who have specific quality expectations and want to protect their assets.
Trends in PV module quality
Al-BSF and passivated emitter rear contact (PERC) solar cells and modules have dominated the market for 20 years, with their own set of module quality issues. The most common of these are:
- Backsheet degradation
- Potential-induced degradation (PID)
- Light- and elevated temperature-induced degradation (LeTID)
- Junction box failure
Backsheet degradation: Backsheet degradation in field-exposed PV modules has been observed and reported for several years and is the major issue affecting the safety and performance of older PV plants with backsheet modules. It is generally acknowledged that a degradation mechanism initiated by front-side UV radiation or along the cell connectors indicates the appearance of thermomechanical stresses.
Chalking and cracks are the most prominent degradation features that can lead to reduced electrical insulation properties and consequently increased electrical hazards. This safety issue, also potentially leading to mechanically catastrophic damage, was primarily caused by poor-quality polymers that were used during a specific period in the early 2010s.
Potential-induced degradation: PID has a variety of root causes for the different types of solar cell technologies. PID-shunting is the most common type of PID in conventional p-type AL-BSF and PERC PV modules. Extensive studies have shown that sodium ions (Na+) under the negatively biased conditions from the glass drift through the SiNx AR coating towards the interface between the Si and the AR coating, and can penetrate into crystal defects crossing the n+-p junction.
This results in significant shunting of the cells and degrades their efficiency and module power output. PV plants with high levels of PID in their modules led to catastrophic drops in energy production and revenue, leading to the eventual replacement of large quantities of modules.
Light- and elevated temperature-induced degradation (LeTID): Light-induced degradation (LID) is a common phenomenon that leads to efficiency degradation of crystalline silicon solar cells. The degradation rate of LID is relatively fast and can lead to saturation within a few days.
The mechanism of LeTID in crystalline silicon has also been intensively studied. Current research shows that the cause of LeTID may be related to hydrogen or other impurities, such as metals contained in crystalline silicon solar cells, but the specific cause of LeTID has not been determined. During heat treatment, hydrogen trapped in the dielectric layer is released, which can passivate most of the defects and improve the efficiency of the solar cells.
However, recent studies have shown that hydrogen-related association and dissociation processes may affect LeTID. While the degradation due to LeTID can be reversible, the impact on energy production before detection and correction can be significant for PV plants.
Junction box failure: Junction box reliability is one of the most crucial issues for PV modules during verification testing and operation in the field. Not only does it have a high failure ratio among various faults, but it usually accompanies severe safety and warranty problems during the PV system lifetime. Burnt bypass diodes have been reported as the top failure of the module in the laboratory and field.
The breakdown point at the PN junction chip is commonly considered the root cause for this failure, which results in energy over-stress and consequently evolves into a burnt junction box. Besides this root cause, improper cable welding and wiring demonstrates that it induces arcing initiated by a strong electric field (bigger than the breakdown electric field for molecules) with small gap distances between the cable and the metal contact.
In order to mitigate these risks, PI Berlin recommends laboratory testing as part of the qualification process to evaluate the reliability of PV modules quality issues related to backsheets PID, and LeTID. Based on these results, uniquely tested bills of materials (BOM) should be agreed upon during the procurement phase and verified using material compliance checks during production supervision.
Current trends
Over the past ten years, PI Berlin has independently assessed the quality of more than 100GW of modules from over 100 PV manufacturers, gaining valuable insights into manufacturing and product quality trends within the PV industry.
A remarkable fluctuation of annual defect rates has been observed in the graph below from 2016 to 2022. The PV module industry maintained a lower defect rate (0.65%) in 2016 due to the maturity of Al-BSF polycrystalline silicon solar cell module. Monocrystalline PERC silicon solar cell modules and new technical innovations in materials, processes and equipment, such as glass-glass modules and bifacial modules resulted in an increase in quality issues and PV module defects.
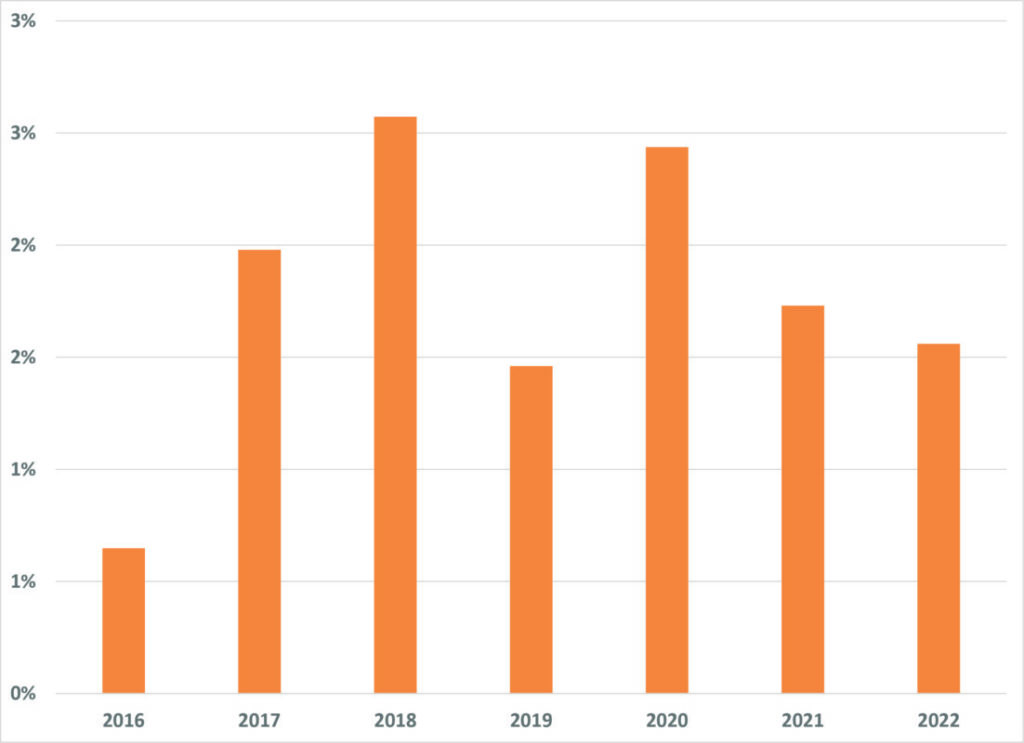
As monocrystalline PERC solar cell modules matured, defect rates decreased, until a rapid shift in larger wafer and multi-busbar technology generated increased module defect occurrences in 2020. Typically, module manufacturing has several processes that introduce risk to module quality.
By analysing the source of defects shown in the graph below, rework, lay-up, cell soldering, EL imaging and framing are identified as top-five defect sources. Together they contribute to >65% of total defects in the module production line.
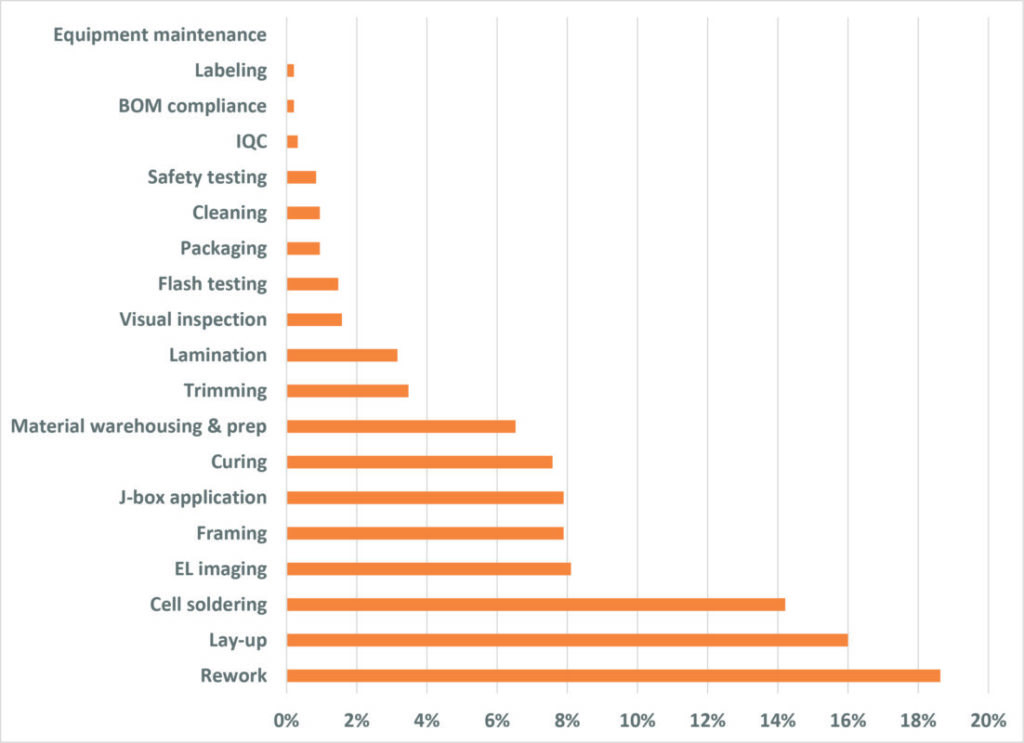
Rework and lay-up replaced cell soldering as the most common major contributor during the past two years. This trend proves that glass-glass and larger module formats increased the impact on module production lines and were the cause of many of the quality defects. As multi-busbar soldering technology becomes more mature and stable, cell soldering will likely no longer be the top module quality issue.
New challenges observed
As PI Berlin looks to the future of module technology and manufacturing, there is real value in understanding historical trends and being able to apply that knowledge in assessing and predicting upcoming patterns. Being able to access and observe changes in production and technological innovations gives us an insider’s perspective on potential upcoming trends. By combining that with our expertise in how trends take shape, we are better prepared to evaluate and forecast changes in module performance.
Here are some of the main issues we see coming in the near future:
- Rapid technology change without long-term reliability test results
- New soldering technologies such as conductive glue, low-temperature soldering and zero busbar overturn the requirement of soldering
- Extreme cost reduction of raw materials, such as thinner glass, thinner encapsulant materials, copper plating for metallisation, silver-coated copper pastes etc.
- Extreme high throughput of production causes a narrow process window
- Thinner but larger wafers require longer and more complicated process steps
- Personnel are inexperienced with process and quality controls due to the aggressive capacity expansion of manufacturers
Challenges and potential risks occurring during this transition may not be caught by manufacturers’ quality management systems. Hiring a third-party quality assurance firm is necessary to maintain the production of a quality product.
Glass in focus
In 2023, around 40% of the modules manufactured were glass-glass modules, and it is expected that this will further increase to 70% over the next few years, according to the ITPV Roadmap Report 2023. The shift towards glass-glass modules was intended to bring many advantages, including humidity resistance, bifaciality and reliability. The reliability aspect was expected due to the rigidness of the glass on both sides, rather than the more sensitive polymer backsheet. Backsheets experienced various levels of degradation over the years depending on the materials used and the local environmental conditions.
Unfortunately, due to many factors that will be addressed below, glass breakage on site after installation has become a significant issue in the industry that must be addressed. PI Berlin has been involved in a number of PV plants over the last two years investigating the root cause of these failures. The failure rate in these PV plants was between 1-10%, and the 10% was found in a 150MW plant. The importance of focusing on the glass as part of the independent quality assurance process has become more critical.
The first factor affecting the reliability of glass-glass modules is module design, in particular the size of the modules themselves. PI Berlin’s primary experience with glass-glass modules in the past was with thin-film modules. Compared to those modules, the current modules on the market are up to four times larger, and on average modules have doubled in size in the past ten years.
The introduction of half-cut cells and the butterfly architecture requires three holes in the rear glass for the junction boxes. In addition, glass thickness has been reduced, as well as the frames, while also shortening the mounting rail or clamp position. All these design factors result in a less rigid module, which is becoming a critical load bearing part of the mounting structure.
The second critical factor is the glass design and quality. Glass/backsheet modules used 3.2mm fully tempered glass, which has high flexural strength and a larger range of temperature change resistance. The glass-glass modules currently on the market use 2mm (or even thinner) heat-strengthened glass, which has almost 50% lower bending strength and temperature resistance. Due to the increased demand in glass and stresses on their supply, the industry sometimes uses non-solar glass for the rearside and also more suppliers are required who may not have the same level of quality as more experienced suppliers.
As part of the investigations into glass breakage, a third factor arose which is the gap in the testing and certification of glass for modules. As glass in the past was not considered a reliability issue in previous module designs, little attention was paid to the specification and test requirements of the glass itself. Since there are no PV-specific glass test standards, questions have come up over whether the safety factors and minimum test loads applied for the mechanical load test of modules are sufficient.
In addition, with the variety of mounting structure designs and tracker systems used in combination with the local loading characteristics, the single module testing method is insufficient to represent actual operational conditions.
Finally, several other factors have been identified during PI Berlin’s investigations that have resulted in glass breakage. Other module defects, such as hotspots caused by shunting, poor soldering or cell breakage, have led to glass breakage due to the extreme localised temperatures. Improper installation due to wrongly applied torque values has caused cracks in the glass originating from the clamps.
Extreme weather conditions have also been the cause in some cases, such as excessive hail events and heavy snow conditions. With the increasing volatility and intensity of weather events due to climate change, it is expected that the resiliency of the modules under such harsh conditions will become more of an issue.
With hundreds of gigawatts of glass-glass modules already in operation and terawatts to be installed in the coming years, our industry will have to pay much more attention to the glass component of modules during quality assurance. Starting at the pre-qualification level in the procurement process, module manufacturers need to provide more information about the glass being used and the testing they have undergone to meet the local conditions of the PV plant.
The industry must develop and adopt testing standards and certification specific to glass applications for solar. Module testing has to continue to develop beyond the current standards to ensure
they are relevant for the current size and design of glass-glass modules.
Finally, the quality control conducted by manufacturers and the quality assurance provided by third parties needs to be expanded to focus more on the incoming glass inspection and controlling of edge treatment and hole drilling during production. Only with strong cooperation between module manufacturers, glass suppliers, testing laboratories and research and development (R&D) institutes will the solar industry be able to ensure the reliability of glass-glass modules in the coming decades.
Silicon supply chain requirements
The role of quality assurance has continued to develop not only at a purely technical level but also to include topics related to sustainability and environmental, social and governance (ESG). Investors and purchasers of solar PV equipment want to ensure that the products they source and the suppliers comply with stringent ESG policies. Legislation in the US and EU regarding due diligence and supply chain traceability has put additional pressure on the industry. In particular, the sourcing and refinement of polysilicon in PV modules have come under international scrutiny based on suspicions of forced labour being used.
To address these concerns, buyers are increasingly seeking independent verification of the origin and production of materials used in the modules and their assembly. Quality assurance providers like PI Berlin have been asked to conduct supply traceability and ESG audits to assess the risks that the modules involve a supply chain that is not consistent with their company’s ESG policies or legislation, and may potentially be seized or blocked on import from overseas.
Over the last two years, PI Berlin has conducted over 30 such traceability audits in module manufacturing facilities in China and across Southeast Asia. Initially, the manufacturers were not well prepared to cooperate in such audits, as they had no dedicated teams or training regarding this topic, there were concerns around confidentiality and their traceability systems were inadequate to track the chain of custody of the polysilicon.
In the last year or so, the larger manufacturers, in particular those with a high level of vertical integration, have drastically improved their traceability systems and have established internal teams who are well versed in the ESG requirements of investors. These manufacturers are now taking proactive steps by contracting independent ESG and traceability audits for their module factories. They have also managed to shift their silicon supply chain completely from the regions of most concern for potential forced labour cases.
As a result, the focus of the quality assurance provider has shifted to integrating the supply chain traceability assessment into the inspections taking place during module production for specific projects. Here, the role of the inspector is to verify that the bill of materials for the main components in the buyer’s module supply agreement is not only certified but also that the origin of the silicon-related components (i.e. cell, wafer, ingot, polysilicon and MGS) can be confirmed.
While some manufacturers are able to provide clear evidence down to the polysilicon supplier through their procurement systems and documentation, others rely on making self-declarations while they continue to improve their traceability capabilities.
Continued progress in the area of ESG and traceability is expected to be made through the Solar Stewardship Initiative (SSI) which was founded by SolarPower Europe and Solar Energy UK in 2021. The SSI is a multi-stakeholder initiative that includes investors, manufacturers, NGOs and other critical stakeholders in the industry, to foster responsible production, sourcing and stewardship of materials in the global solar value chain.
An ESG Standard has already been established in 2023 and a Traceability Standard will be developed in 2024. These standards will give both buyers and manufacturers clarity on the requirements for the industry and comfort that the products used in PV projects meet these requirements.
Conclusion
Undeniably, new technologies and new materials have an immense impact on every facet of solar PV modules. The continuous increases in conversion efficiency and further cost reduction serve as a catalyst for innovation and improvement. On the other hand, these rapid changes over the last few years present also challenges in terms of the manufacturing quality of modules. Past experience has shown how the industry has paid a high price for premature degradation defects affecting their investments, such as PID and backsheet cracking.
The latest technologies are bringing their own new challenges such as insufficient soldering strengths and glass breakage. Independent quality assurance plays a crucial role in managing these risks from the product qualification process to the manufacturing in the factory and until the modules meet the delivery site.
Furthermore, buyers and manufacturers have new requirements with respect to ESG and supply chain traceability that introduce new challenges in terms of sourcing materials, adapting procurement systems and increasing transparency. The solar industry is known for its incredible ability to change and improve at an astonishing pace, and quality assurance will continue to accompany this growth to protect the expected growth in the future.
Fei Lu leads factory services for PI Berlin, a member of the Kiwa Group worldwide, including auditing and production supervision of PV and battery storage systems. Previously, Lu served as director of module technology at the Chinese corporation Jiangsu Linyang Photovoltaics Technology and prior to that as senior engineer and project lead for product development at REC Solar in Singapore.
Steven Xuereb is an executive director of PI Berlin, focusing on delivering independent engineering services for large-scale solar plants. Before joining PI Berlin, he spent eight years procuring and developing solar and wind projects in North America, Chile and South Africa for Airtricity and Mainstream Renewable Power. His experience in the industry includes greenfield development, acquisitions, contracts management, research and development, certification and service operations. He is a mechanical engineer with a master’s degree in renewable energy from the Universities of Oldenburg and Kassel.